Concrete batching equipment: 100% custom systems
Concrete batching equipment from JEL Manufacturing will keep your batch plant working smoothly and safely. In addition to repair parts, we also offer silos, bins, hoppers and control systems to expand/improve your existing plant. Just like our concrete batch plants we also custom build feed systems, hoppers, conveyors and bins to make your batching plant as profitable as possible.
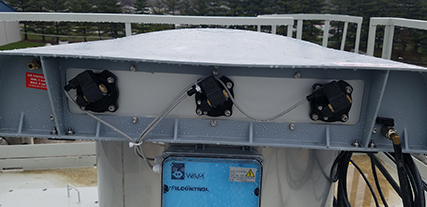
Dust Collectors
Collect dust from the inlet zone in dry batch plants during truck mixer filling. Silotop dust collectors, too.
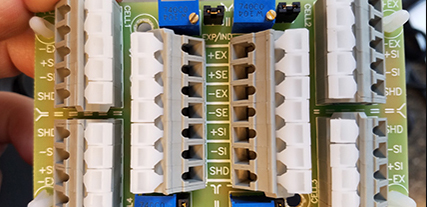
Batch Plant Parts
Our partner FESCO Direct works with manufacturers nationwide to provide the highest quality batch plant parts.
For concrete batch plant equipment, contact FESCO Direct
JEL Concrete Plants is a premier manufacturer of batching plant bins, hoppers, conveyors and control systems for batching plants. If you're looking for additional components like wear parts, water heating & cooling, reclaimers, and other parts, contact FESCO Direct for sourcing & distribution.